Pesquisadores da UFLA desenvolvem adaptador que converte máscaras de mergulho em máscaras para respiradores hospitalares
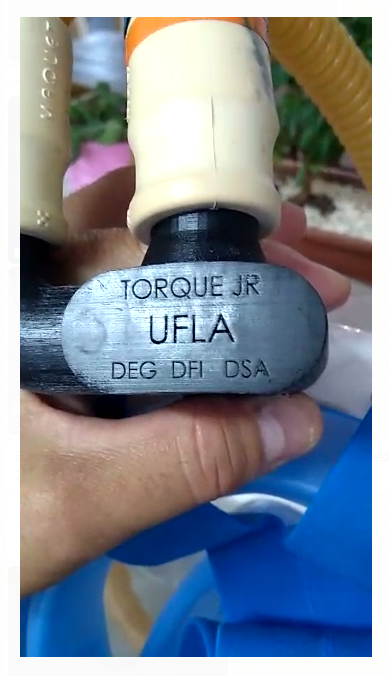
A Universidade Federal de Lavras (UFLA) continua, ininterruptamente, trabalhando em projetos e pesquisas que possam contribuir e auxiliar no enfrentamento a pandemia do novo coronavírus. Parte das ações desenvolvidas pela Instituição é através da criação de equipamentos que beneficiam diretamente a população. A partir da iniciativa da Empresa Júnior de Engenharia Mecânica, Torque Jr, juntamente com o auxílio do coordenador do curso de Engenharia Física, professor Jefferson Esquina Tsuchida, do Departamento de Física (DFI) e do professor do Departamento de Ciências da Saúde (DSA) Hélio Haddad Filho, foi desenvolvido um adaptador para converter máscaras de mergulho em máscaras para respiradores mecânico, que irá beneficiar não só os profissionais da saúde que estão atuando na linha de frente, como também levará maior comodidade aos pacientes infectados pela Covid-19. A previsão é que sejam produzidos 30 conjuntos para doação e utilização no atendimento a pacientes assistidos pelo Sistema Único de Saúde em Lavras.
Acompanhe a entrevista, feita pelo Núcleo de Divulgação Científica (NDC/UFLA), com o professor Jefferson:
O que é esse adaptador?
Um dos grandes gargalos que existe hoje no tratamento da Covid-19 não é apenas os respiradores, mas sim as máscaras que são utilizadas nesses aparelhos. A máscara convencional é usada para auxiliar na respiração de forma mecânica, contudo ela não prevê a questão da isenção do contágio á partir da expiração. Isso é um grande problema, principalmente para os profissionais da saúde que estão trabalhando na linha de frente.
Então adaptamos uma máscara de mergulho, conhecida como Full Face, que cobre todo o rosto e é totalmente vedada. Criamos um adaptador para que o ambiente interno da máscara não contamine a atmosfera externa, ou seja, o ambiente onde o paciente infectado se encontra. Quando a pessoa expira, o ar sai por um tubo e volta para o respirador ou para um filtro, que vai conter os aerossóis, pequenas gotículas que são um dos principais fatores responsáveis pela transmissão do vírus.
Dessa forma, o adaptador faz a conversão de uma máscara de mergulho para uma que pode ser utilizada em respiradores. Isso gera uma grande economia, uma vez que uma máscara hospitalar, de face inteira, custa em média 2mil reais, enquanto esse modelo adaptado fica em torno de 400 reais. Ressalto aqui que a máscara de mergulho já se encontra pronta no mercado; desenvolvemos apenas o adaptador.
Como ele foi desenvolvido?
Ele foi desenvolvido a partir de uma ideia que surgiu na Itália. Uma empresa do ramo de mergulho fez uma grande doação de máscaras, que foram adaptadas. Então pegamos o esboço inicial desse adaptador e adequamos às máscaras que estão disponíveis no mercado brasileiro. Optamos por trabalhar com material nobre: uma resina que é ideal para aplicações que exigem função rígida com flexibilidade moderada, sendo um material biocompatível, utilizado em aplicações médicas. Dessa forma, aperfeiçoamos o projeto para que a quantidade de material usado fosse a menor possível, visto que ele possui um custo elevado.
Poderia resumir os benefícios desse adaptador?
Podemos citar dois grandes benefícios a partir do desenvolvimento desse projeto. Como é possível controlar a expiração, ou seja, o ar que sai dos pulmões, conseguimos direcionar esse ar sem que ele vá para o ambiente externo, o que diminui consideravelmente o contágio, especialmente pelos profissionais da saúde.
Outro grande benefício é que a máscara utilizada é de face inteira, o que traz maior comodidade para a pessoa infectada, já que o outro modelo cobre apenas nariz e boca, gerando certo desconforto e dificultando muito o diálogo entre paciente e médico, em especial os pacientes idosos.
Resumindo, essa máscara de face inteira diminui a sensação de claustrofobia, impede que o ar da expiração contamine o ambiente e permite uma boa comunicação entre paciente e médico.
O que levou a equipe a desenvolver esse projeto?
Poder ajudar os profissionais que estão na linha de frente ao combate contra a Covid-19 foi nosso principal foco.
A partir daí, fui procurado por membros da empresa júnior de Engenharia Mecânica Torque Jr, que formaram uma equipe multidisciplinar, reunindo professores do Departamento de Ciências da Saúde (DSA) e do Departamento de Engenharia (DEG). O grupo resolveu desenvolver esse adaptador para a máscara, pois notamos que é um grande problema que existe quando se está na linha de frente do combate à pandemia do novo coronavírus. Então, após diversas pesquisas realizadas pelos estudantes que fazem parte da Torque Jr, o adaptador foi projetado com o auxílio dos professores.
Qual custo do equipamento?
O conjunto completo, máscara e adaptador, fica em média em 400 reais, sendo que o custo da máscara é em torno de 150 reais.
Inicialmente o custo parece alto, contudo o processo de Impressão 3D que estamos utilizando garante uma alta produtividade, fabricando cerca de 18 unidades por dia.
Qual é a meta para esse projeto?
Temos como meta inicial a produção de 30 conjuntos de máscara e adaptador para serem doados aos hospitais da cidade para utilização em pacientes atendidos pelo Sistema Único de Saúde do município. Com esse quantitativo iremos cobrir todos os respiradores, atualmente disponíveis em Lavras, e cada local ainda contará com algumas unidades reserva.
Que outras informações sobre os procedimentos seguidos vocês podem destacar?
A primeira etapa do projeto foi o desenvolvimento do desenho em 3D. Essa fase foi totalmente desenvolvida pelos alunos da Torque Jr., sob a minha supervisão. A etapa seguinte foi a impressão de modelos de teste para a validação dos encaixes do adaptador na máscara e nas mangueiras do respirador. Utilizamos o método de impressão 3D FDM, em que um filamento de um polímero é fundido e extrudado camada a camada. Após alguns modelos de teste impressos, conseguimos chegar em um modelo de adaptador com um design mais compacto. Na fase seguinte, fizemos a impressão do modelo final em resina, utilizando um processo de Impressão 3D chamado de SLA ou estereolitografia, em que a peça é impressa camada a camada. Inicialmente é impresso um molde em cera e, sequencialmente, é depositada a resina, que é curada por um laser ultravioleta, e esse processo se repete camada a camada. É um método que garante que o modelo impresso é 100% idêntico ao desenho 3D projetado.
Optamos por utilizar o método de impressão 3D SLA por alguns motivos importantes: maior produtividade, sendo cerca de 18 unidades/dia; o material utilizado é biocompatível e possui rigidez e flexibilidade adequadas para a utilização proposta e o modelo é totalmente fiel ao desenho 3D. Já o método FDM é mais barato, contudo possui algumas desvantagens: cada modelo leva cerca de 14 horas para ser impresso, o material pode deformar durante a impressão e o modelo final ainda pode ficar frágil. Contudo esse último método ainda não foi descartado. Atualmente estamos testando outros tipos de filamentos para verificar se conseguimos obter um modelo mais resistente e fiel ao desenho 3D.
A equipe envolvida no projeto é composta pelos pesquisadores: professor do DFI Jefferson Esquina Tsuchida (coordenador da pesquisa); professores do DSA Hélio Haddad Filho e Joziana Muniz de Paiva Barçante; professor do DEG Sandro Pereira da Silva e estudantes de graduação da Torque Jr: Murilo da Silva Carrara, Vitor Luchetta Parra, Alexandre Guimarães Lara e Felipe Queiroz Cavalcanti Brasil.
Texto: Caroline Batista, jornalista - bolsista / Dcom
Edição do Vídeo: Luiz Felipe - Dcom/UFLA